Vacuum-assisted cold chamber die casting machine
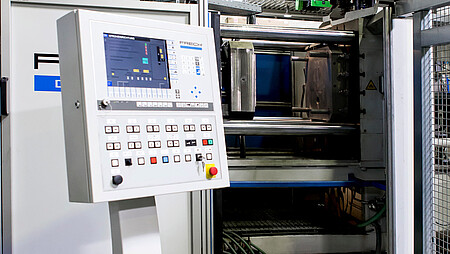
The Frech DAK 350-40 cold chamber die casting machine is suitable for processing aluminum and magnesium casting alloys. It has vacuum support, which enables the production of low-porosity die-cast parts. With the help of the automatic mold spraying device, a near-series process is also possible. In addition to the use of customer-specific mold tools, various molds can be used at the IW to produce sample and model geometries.
The Frech DAK 350-40 cold chamber die casting machine is suitable for processing aluminum and magnesium casting alloys. It has vacuum support, which enables the production of low-porosity die-cast parts. With the help of the automatic mold spraying device, a near-series process is also possible. In addition to the use of customer-specific mold tools, various molds can be used at the IW to produce sample and model geometries.
Description of the system
The individual components form a casting cell for processing aluminum and magnesium alloys in die casting. By using a dosing furnace for aluminum alloys and a furnace system for magnesium alloys, materials can be processed semi-automatically in industry-standard quality. The real-time controlled Frech DAK 350-40 cold chamber die casting machine enables the casting of components up to a volume of approx. 1908 cm³. Up to 4 controlled oil-heating-cooling circuits can be used thanks to the two heating-cooling units. 8 controllable water circuits are also available for mold cooling. All standard measurement and analysis processes can be implemented and equipment is available in-house for initial sampling and series production as well as for alloy development and research. The mould is also linked to a vacuum system and can be evacuated to a pressure of up to 50 mbar in order to minimize pores in the component.
Technical data:
-
Processing of Al and Mg alloys (dosing furnaces)
- Scooping device for processing small quantities of molten aluminum
- Furnace systems available for small quantities of molten Mg
- 3700 kN locking force, max. blast area 1233 cm² (300 bar)
- Pouring volume up to 1908 cm³, pouring force 409 kN
- Form clamping area: 940 x 1095 mm
- 4 controllable oil heating/cooling circuits, 8 controllable water circuits
- Complete sampling including analysis and measurement technology as well as in-house research possible
30823 Garbsen