CURRENT RESEARCH PROJECTS
- Development of TLP solders for brazing copper and steel materials at 750 to 850°C
- Development of a brazing-nitriding hybrid process in a continuous furnace for the serial production of water-cooled bipolar plates made of chrome-plated materials
- Silane-doped process gases for the generation of vacuum-adequate process conditions in inert gas continuous furnaces
- Clarification of the mechanisms for surface activation during flux-free brazing of high-alloy steel materials under inert gas and in a vacuum
- Influence of brazing process atmosphere and process time on the fatigue limits of high-temperature brazed CrNi steel joints
- Development of a continuous inert gas furnace process with heat recovery ventilation
Facilities:
- Inert gas continuous furnace from Kohnle for process temperatures up to 1200 °C in N2/H2/Ar atmosphere with/without silane mixing
- Hochvakuumofen mit Schnellabkühlung von der Fa. PVA für Prozesstemperaturen bis 1250°C
- Sliding-table flame brazing system with 6 burners from Everwand & Fell
- Testing facility for inductive brazing in shielding gas with variable shielding gas mixture for the operation with/without silane-containing process gases
- Various batch furnaces for heat treatment in air or in shielding gas
Facility Specifications Soldering Technology
Tubular Furnace
For laboratory tests under variable process gas conditions, IW operates a tubular furnace with quartz glass muffle, automated gas mixing device and furnace control at the site in Witten. Heat treatments up to 1100°C can also be carried out here with reactive process gases.
Induction Brazing Machine
Induction brazing tests are carried out in a self-built laboratory facility. The testing facility is suitable for inductive brazing in protective gas and is equipped with a variable protective gas admixture for operation with/without silane-containing process gases for this purpose. The components are heated with a water-cooled inductor, which is operated by means of an RF generator with an adjustable frequency range between 50 and 450 kHz and a maximum power of 3000 W (i-class 1.5/3 kW, Cobes GmbH, Weisweil, Germany).
CONTACT PERSON FOR JOINING TECHNOLOGY – BRAZING AND THERMAL PROCESS TECHNOLOGY
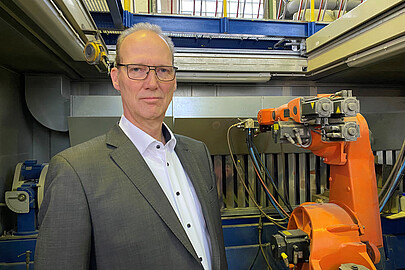

58453 Witten
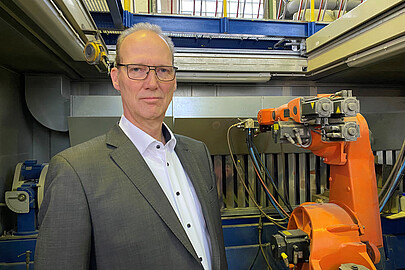

58453 Witten